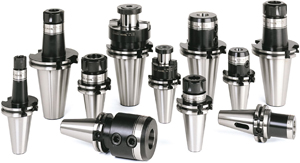 |
MONOd' and MONOforce
QUALITY, PRECISION, STRENGTH, AND CONVENIENCE
The integrated MONOd’ and MONOforce toolholders
represent an ideal solution to equip any type of machine tool with HSK
63, DIN AD+B, BT AD+B and CAT base arbors, guaranteeing the benefits of
a high quality, high precision and ultra-tight tool, with a price that
is highly competitive on the market. The MONOd’ program includes ER
collet chucks, Weldon, mill holders, Morse tapers, and tapping chucks.
The MONOforce ultra-tight line involves tool housing dimensions of Ø
.47",
.79" and 1.26", and allows for the tool to be tightened from Ø .12" to
.98"
with the use of standard reduction bushes. MONOforce is also available
in kits complete with reduction bushes and tightening spanner.
|
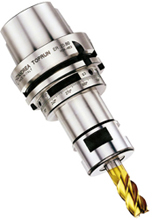 |
TOPRUN
HIGH SPEED, BALANCING, AND PRECISION
A balanceable monobloc toolholder system that
guarantees high precision in high speed machining on modern machining
centers. The concentricity between the base arbors HSK 63, DIN, BT and
CAT and the seat of the tool is always less than 3 µm. The advantages of
using TOPRUN are the precision and the better quality surface finishing,
a longer life of the tool and the machine spindle, as well as reduced
costs and times and less noise and vibrations. The TOPRUN toolholder
line includes ER collet chucks, Weldon, mill holders, and FORCE, an
ultra-tight milling force.
|
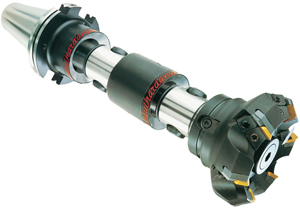 |
MODULHARD'ANDREA
MODULARITY AND HIGH PRECISION
High precision modular toolholders for machine tools
and machining centres that allow for boring, milling, drilling, and
tapping operations to be carried out with extreme flexibility and
rigidity. The cylindrical-conical coupling comes in nine sizes, ensuring
the interchangeability of all the elements of the system that includes
the base arbors HSK, DIN, BT, CAT and Polygon-shank, toolholder
extensions, reductions, and adapters. The complete boring program for
machining diameters from .10" to 110.24", complete the MHD’ line complete
with roughing double-bit heads and centesimal and micrometric Testarossa
finishing heads with a 2µm sensitivity adjustment.
|
 |
GRINTA and MCD'
MILLING AND TURNING OPERATIONS
D’Andrea solutions for
milling and turning operations that use cutting geometries with ISO
inserts. The GRINTA program takes advantage of the perfect coupling
concentricity and the extreme resistance to torsion of the MHD’ modular
attachment. The arbors from Ø .63" to 1.26" are built with the MHD’
cylindrical-conical attachment and threaded end, while the one with Ø
from 1.57" to 2.48" are made with the MHD’ integral attachment.
The MCD’ line includes lathe tools and toolholders, made in accordance
with HSK-A63 standards with ICTM construction tolerances recommended for
the application on MULTI-TASK machines. The program is produced in
modular versions, with HSK attachment and interchangeable insert holder
seats and complete with toolholders that permit the mounting of standard
lathe tools.
|
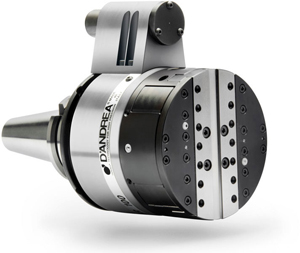 |
TA-CENTER
TURNING OPERATIONS ON ALL MACHINING CENTRES
Boring and facing heads with automatic balancing,
that allow for turning operations with fixed pieces on all machining
centers. Built in five models with Ø of 3.15", 3.94", 4.92", 6.30", and
7.87",
they can be easily applied on any machining center set up with a command
unit for controlling the feed of the toolholder slide. The dimensions,
structure, and weight of some models, allow for the TA-CENTER to be
positioned even in the tool magazine area of small machining centers and
loaded by the tool changer on the spindle of the machine. The simple
application of the U-DRIVE command unit connected to the machine NC,
allow for all types of operations to be performed including turning,
cylindrical and conical boring, facing, threading, corner rounding, and
spherical operations.
|
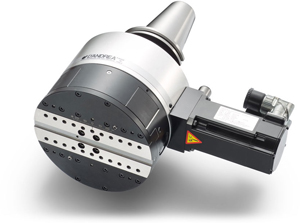 |
TA-TRONIC
TURNING OPERATIONS ON ALL MACHINE TOOLS
Boring and facing heads with automatic balancing,
that allow for turning operations with fixed pieces on all machine
tools. Built in four models with Ø of 3.94", 4.92", 6.30", and 7.87", they
can be easily applied manually or automatically on boring machines,
machining units, and special machines. Connected to the NC of the
machine tool they make it possible to perform all types turning,
cylindrical and conical boring, facing, threading, corner rounding, and
spherical operations. Application on machines where they cannot be
connected to the NC, may be made by managing the motor with a practical,
simple, and economical positioner complete with a wireless
REMOTE–CONTROL.
|
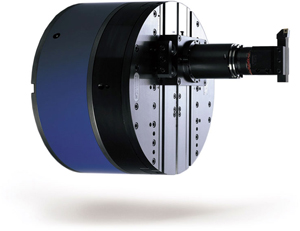 |
U-TRONIC
"SUPER SIZED" PERFORMANCE
Medium and large sized boring and facing heads,
which allow for turning operations to be made with fixed pieces on all
machine tools. Built in various models from Ø of 14.17" to 63", they
can be applied manually, automatically, and with pallet systems on
boring machines and special machines. Connected to the NC of the machine
tool, they make it possible for all types of operations to be made
including turning, cylindrical and conical boring, facing, threading,
corner turning, and spherical operations. Managing machines where a
connection to the NC is impossible, may be made using a positioner with
a wireless REMOTE–CONTROL. Special versions of U-TRONIC, with two slides
or with counterweights for self-balancing may be supplied upon request.
|
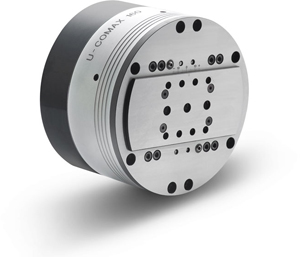 |
U-COMAX
UNIT AND TRANSFER SOLUTIONS
U-Comax boring and facing heads are axial command
heads designed to be used on transfer machines, machining units, and
special machinery. Even during rotation the feed control of the
toolholder slide is commanded by a U-Drive drive unit, mounted behind
the spindle and managed directly by the NC of the machine tool. U-Comax
heads are used for inner facing, outer facing, back-facing, inner and
outer turning operations, grooves, phonographic grooves, cylindrical and
conical threading, conical and variable boring, concave and convex
corner rounding, through interpolation with the other the machine axes.
|
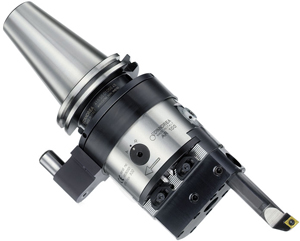 |
AUTORADIAL
FOR AUTOMATIC FACING
Facing heads with automatic feed and rapid return
of the slide, without stopping or inversion of the machine tool spindle.
Built in three models, AR100, AR125, and AR160, that are easily applied
on machining centers, processing units, and on NC machines and do not
require any electronic interface or servo drive. They automatically
perform a work cycle of facing, back-facing, phonographic grooves on
flanges, internal or external seats for snap rings or O-Rings. Six feeds
of the interchangeable tool holder slide are available, upon request.
|